In the realm of engineering, structural integrity and performance are paramount. At Graphler Technology Solutions, our commitment to delivering cutting-edge analyses ensures that every project achieves its full potential. Recently, we undertook an extensive finite element analysis (FEA) of a Strap U-Frame. This blog delves into the highlights and insights from the study.
Objective of the Study:
The primary goal of the FEA was to evaluate the structural behavior of the Strap U-Frame under a variety of operational loads and conditions. This included assessing how the U-Frame responded to forces induced by tension in the strap, moments generated during operation, and reaction forces from components like the crank and pawl. By simulating these real-world conditions, the analysis aimed to:
- Identify Critical Stress Points: Determine locations within the U-Frame where stress exceeded safe operational thresholds, particularly areas prone to potential cracking or fatigue failure.
- Examine Deformation Patterns: Evaluate how the structure deforms under load to ensure that any displacements remain within acceptable limits to maintain functionality.
- Validate Material Performance: Analyze whether the materials selected for the U-Frame and its components could withstand the applied loads without permanent damage or failure.
- Guide Design Improvements: Provide actionable insights for optimizing the design and material usage to enhance durability, safety, and cost-effectiveness.
This holistic approach ensured that the U-Frame design met stringent performance standards while aligning with the operational demands and longevity expectations of the client.
Analysis Setup
The analysis focused on multiple load cases, including:
- Belt Tension: Simulated at 26688 N, generating a significant moment of 1334400 N-mm.
- Force Transmission: Evaluated through the crank lever requiring a force of 3587.10 N for operation.
Boundary conditions, material properties, and operational loads were meticulously configured to replicate real-world scenarios.
Key Findings
1. Deformation Analysis
- Maximum deformation observed: 2.93 mm.
- Despite localized deformation, the overall structure maintained functional integrity.
2. Stress Distribution
- U-Frame: Maximum principal stress reached 1032 MPa, exceeding the material’s ultimate tensile strength. However, the stress concentration was confined to the surface peel layer, indicating potential for localized cracking without immediate failure.
- Pawl: Maximum stress of 858.23 MPa surpassed yield strength at contact points. The compressive nature of stress ensured no catastrophic failure.
- Shaft: Surface stress exceeded yield strength but remained within acceptable limits at the core, highlighting resilience against major deformation or breakage.
3. Reaction Forces
The total reaction force on the pawl was calculated at 5239.4 lb, distributed proportionally across compression supports.
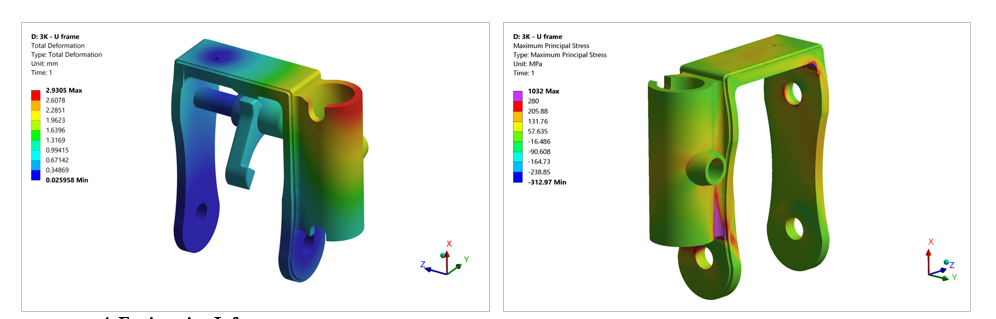
4. Engineering Inferences
- Localized Cracking: Stress concentrations in the U-Frame and Pawl necessitate enhanced surface treatments or reinforcements to mitigate fatigue risks.
- Material Performance: While the materials demonstrated high resilience, exceeding yield thresholds in localized regions requires design refinements.
- Optimized Design: Potential adjustments in geometry or material distribution can enhance load-bearing capacity without significant weight increases.
Graphler Technology is one of the leading product design companies in India. We have experts in FEA services and also we are specialized in CFD consulting services, structural design services, 2D to 3D Conversion services, stress analysis services etc.