The field of aerodynamics plays a critical role in the automotive industry, as it directly impacts a vehicle’s fuel efficiency, speed, stability, and overall performance. At Graphler Technology Solutions, we recently conducted an aerodynamic simulation of a passenger car to assess and optimize its aerodynamic performance. Here’s an overview of the key elements of this study and its outcomes.
1.Objective of the Study
The primary goal of this aerodynamic analysis was to evaluate the aerodynamic torsor, which includes both drag and lift forces acting on the car. Additionally, the study focused on the flow features around the vehicle, including the wake and bodywork. These analyses are essential for improving vehicle design by minimizing drag, enhancing stability, and increasing fuel efficiency.
2.Methodology: Wind Tunnel Simulation
The study utilized a wind tunnel simulation setup, with specific boundary conditions replicating real-world scenarios. The tunnel design ensured that the aerodynamic features of the vehicle could be accurately observed:
- Tunnel Front: ~2 times the vehicle length.
- Tunnel Rear: ~3 times the vehicle length.
The boundary conditions included an inlet velocity, pressure outlet, frictionless walls, and a moving belt to simulate ground movement. Additionally, tires, rims, brakes, and air intake were modeled with realistic conditions such as angular velocities and mass flow.
Vehicle Parameters
The vehicle dimensions used in the study were as follows:
- Length (X-axis): 4009.67 mm
- Width (Y-axis): 1996.85 mm
- Height (Z-axis): 1443.07 mm
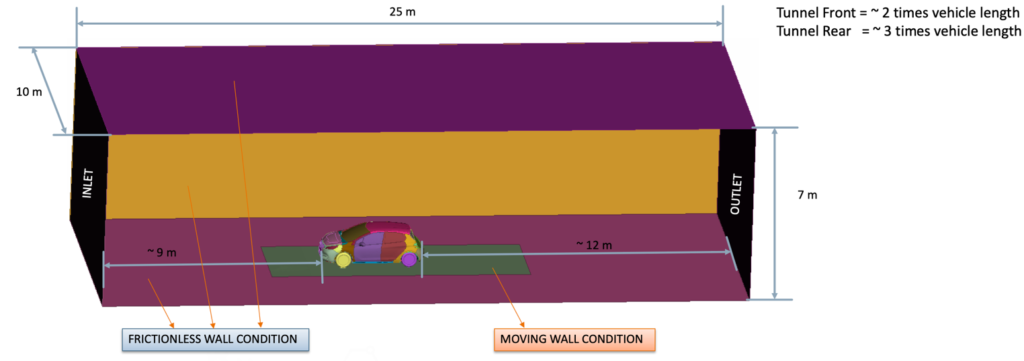
These dimensions were crucial in determining the drag and lift forces experienced by the vehicle during the analysis.
3.Key Deliverables
The outputs of the study offered valuable insights into the vehicle’s aerodynamic performance:
Aerodynamic Torsor:
Global and Discretized Data: The analysis provided both global and specific measurements for the drag and lift forces on various parts of the vehicle.
Bodywork Analysis:
Parts Contribution to Drag and Lift: A detailed breakdown of the aerodynamic forces contributed by different regions of the vehicle, such as the superstructure, wheels, under the hood, and floor, helped pinpoint areas for potential improvements.
- Flow Analysis:
- Pressure Coefficient (CP) Distribution: This analysis was performed along the vehicle’s body to map pressure variations, which influence drag and lift.
- Wake Analysis: The wake region, critical for vehicle stability, was analyzed using tomography. Velocity, pressure, and pathlines in the wake were studied to better understand airflow patterns behind the vehicle.
4.Practical Applications
Understanding how drag and lift forces impact a vehicle allows for more efficient design choices. For instance, reducing drag enhances fuel efficiency, while controlling lift improves vehicle stability at high speeds. Our comprehensive aerodynamic analysis provides the necessary data to make informed design adjustments, whether for mass production cars or specialized racing vehicles.
- Conclusion
Through this simulation, Graphler Technology Solutions continues to demonstrate its commitment to providing innovative engineering solutions. By analyzing and refining aerodynamic performance.
Graphler Technology, one of the best Product Design Companies and CFD consulting services providers. We also specialize in stress analysis services, structural analysis services, and structural design services. For more information on night purging and how you can incorporate it into your next project, please feel free to contact us today.