INTRODUCTION
Heat exchangers are important engineering systems with a wide variety of applications including power plants, nuclear reactors, refrigeration and air-conditioning systems, heat recovery systems, chemical processing and food industries.
Due to the high consumption and reduced availability of fuel resource, high thermal performance heat exchanger have been subject to great interest over decades.
HOW IT WORKS?
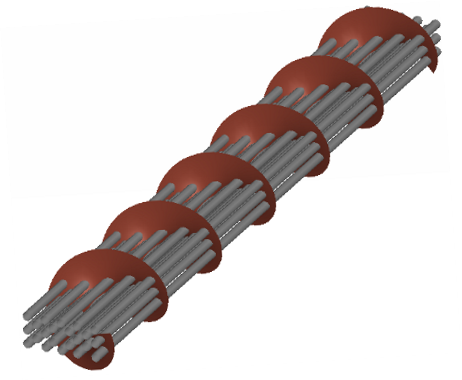
Typically, two fluids with different temperatures circulate through the heat exchanger in natural or forced convection manners and the thermal energy is exchanged via surfaces during the process. There are two primary flow arrangements in the heat exchanger: a parallel-flow and a counter-flow. Two fluids travel from the same end to another end in the parallel flow heat exchanger. For the counter-flow arrangement, the two fluids run in the opposite direction from two ends of the heat exchanger.
When using heat exchangers it is always the possibility that the fouling will occur. Fouling is generally defined as the deposition and accumulation of unwanted materials such as scale, algae, suspended solids and insoluble salts on the internal or external surfaces of processing equipment including boilers and heat exchangers.
NEGATIVE IMPACTS OF FOULING,
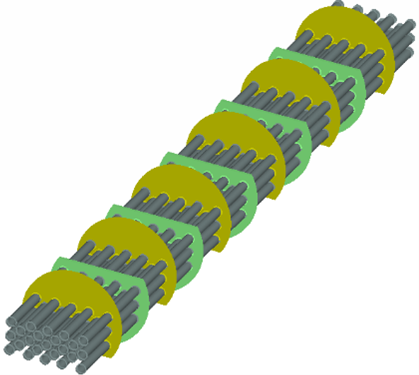
- operational efficiency
- reduces thermal efficiency
- decreases heat flux
- induces under-deposit corrosion
On most industries today, a major economic drain may be caused by fouling. The total fouling related costs for major industrialised nations is estimated to exceed US$4.4 million annually. One estimate puts the losses due to fouling of heat exchangers in industrialised nations to be about 0.25% to 30% of their GDP.
DESIGN CONSIDERATIONS TO DECREASE EFFECTS OF FOULING
There are a number of accommodations a designer may use once they have figured out how much fouling to expect in a particular unit.
A high level of turbulence keeps sediments from settling on the surface of the heat exchanger, and also helps clean off any fouling so it is important to ensure that the design velocities are high enough to mitigate fouling but not too high to promote erosion.
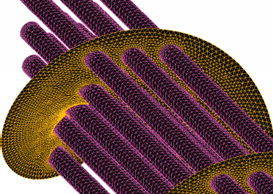
Try to keep a uniformly high velocity throughout the entire exchanger, so that sediments are not able to settle. Keep the amount of low velocity turns and ‘dead’ spots to a minimum, so that fouling will not accumulate. CFD Consulting Services cover a wide range of experience and advice that are for the heat exchange systems improvement.
HOW TO IMPROVE YOUR DESIGN WITHOUT DOING EXPERIMENTS?
Computational Fluid dynamics provides the flexibility to change design parameters without the expense of hardware changes. It therefore costs less than laboratory or field experiments, allowing engineers to try more alternative designs than would be feasible otherwise. It also reduces design cycle time and cost by optimizing through computer predictions. Moreover, it investigates and understands the “why” for existing problem or new equipment.
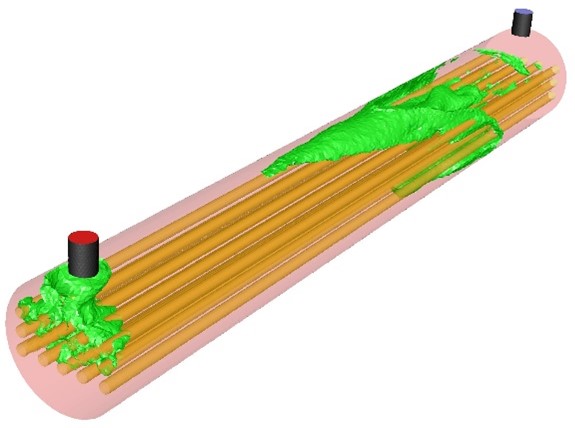
With the increasing trend in which industrial organizations are geared towards sustainability and cost-effectiveness, CFD technologies and Structural Analysis Services are getting to be more of a necessity in the achieving of the objectives.
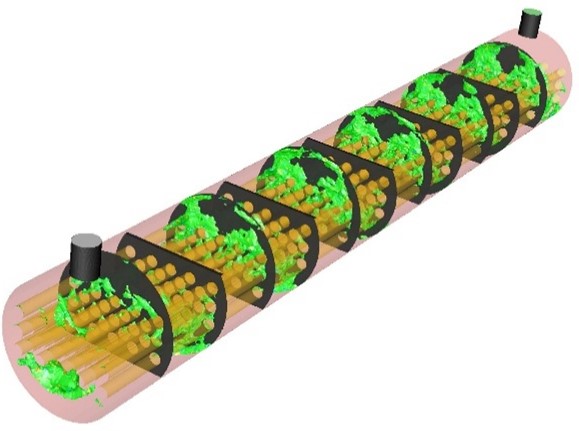
Power of CFD
- Provides better insight and foresight to the problem
- Reduces the total product cycle time
- Cuts the expensive experimental procedures
A computational model has been and solved using commercially available CFD solvers. Two different designs are considered in this numerical analysis.
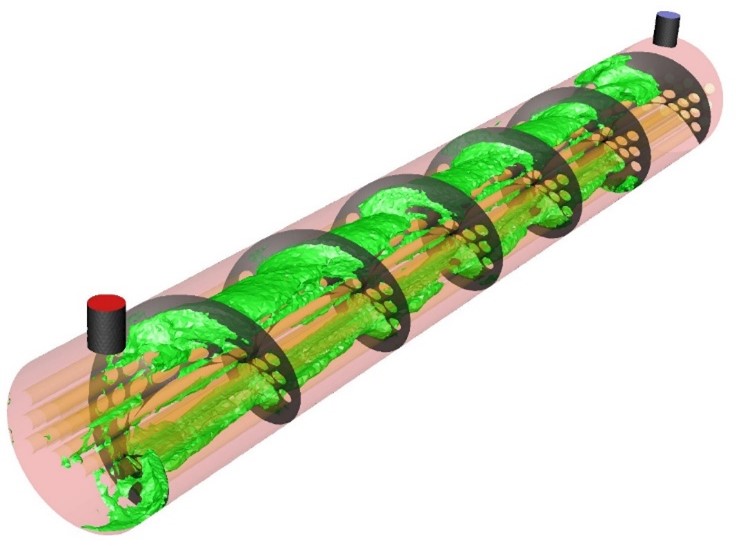
FINDINGS
Baffles were introduced to develop turbulence inside the shell. It is absorbed that the helical baffle provides better cascading effect thus results in increased, uniform eddy dissipation inside the domain (Figure 6 – 15000m2/s3).
Reach out Graphler technology for a Stress Analysis Services .We are also specialized in Structural Design Services and more.