Plastics component are prevalent in consumer and industrial segments for its strength to weight ratio, low cost and ease of manufacturability. They have a clean surface finish, water and UV resistance, chemical resistance and corrosion resistance.
From bumpers in automotive, Computer Peripherals-Mice, keyboards, Medical equipment for its sterility, mobile components, packaging products – plastic component has its footprint.
For a given component, there are many ways to manufacture. Some of the manufacturing processes for plastic parts are
- Casting
- Extrusion
- Compression Moulding
- Forming
- Injection moulding
- Rotational Moulding
- Blow Moulding
- Thermoforming
- 3D Printing
It is vital to build a part around the required functionality, design intent of the end component, weight, model simplification, reduction of components, elimination of assembly and fabrication processes, structural strength, cost reduction and production process requisites. All the built requirements are considered in the part design, tooling, material selection and finishing processes.
Material Selection:
Polymer selection is always a tedious part in the product development phase. Mostly, product engineers rely on the vendors to advise a suitable variant of polymer for the product. Based on the objectives and requirements pledged by the product’s operation and working environment – polymers are selected based on the level of Chemical and UV resistance, Temperature, Heat resistance, Flammability, Electrical and Mechanical capabilities, required surface finish and assembly ease suitable material are chosen. Due to the day by day developments in polymer resins, the feasibility of manufacturing process for the material, its availability and cost are taken into account on selection.
Part Design:
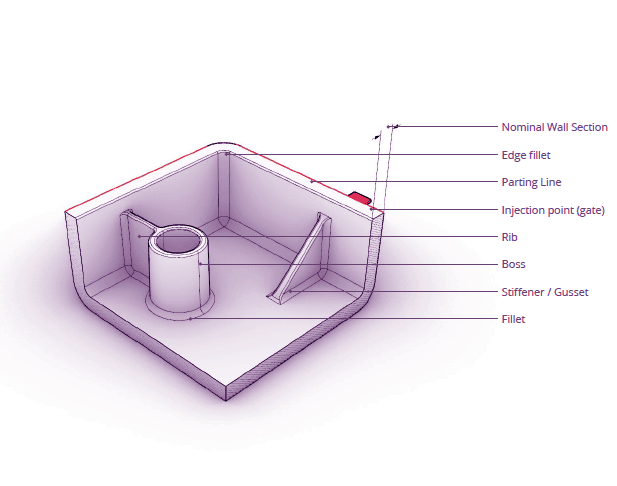
As previously discussed, the built product requirement has to be incorporated from the start of the design. There are certain aspects to be taken care of while designing the part.
Radius: Internal sharp edges have to be avoided while designing the component. All corners and edges are to be filleted and provided with the radius based on the thickness considered and the strength parameters required near the corners. As a general thumb rule, the corners and edges are filleted with a radius of 0.9 to 1.2 times the nominal thickness
Wall Thickness: Wall thickness is a primary element for the strength of the component and is also in the prospect of manufacturability. Wall thickness has to be consistent to avoid most of the defects occurring during the manufacturing processes. In-consistent thicknesses affect mould flow, part formation and cooling. Higher thickness may affect the flow and cooling of the flow. Radius and Rounded corners in the edges help proper filling in the mould.
Draft Angle: Taper in the vertical walls of the component is called the draft angle. Positive draft angle enables proper ejection of the component from the die without damage. As a general thumb rule, the draft angle of 1 to 2 degrees is applied to the inner vertical walls.
Gate Location: Gates ensures proper resin flow and filling of the cavity in the mould. Gates are positioned to effectively fill the cavity in the mould before the resin cools down. Type of gate and its position varies based on the geometric complexity and has a high impact over the feasibility of producing the component without any defects
Ribs: Plastic components with small wall thickness and requires mechanical strength – Ribs are provided to reinforce the walls and to reduce shrinking. To eliminate white marks, 50 to 70 per cent of the wall thickness is considered for ribs.
Mould Shrinkage: Generally, 20 per cent of the volume gets reduced from the cavity due to shrinkage while cooling. Amorphous material shrinks lesser over crystalline polymers. Some of the parameters to consider to avoid shrinkage are – Polymer formulation, mould design, process temperature, melting temperature, cooling temperature, injection speed, time and pressure.
Check out Graphler Technology, leading Product design company in India. We have engineering experts specialized in CAD, Plastic Design, Plastic Part design, Surface modelling, 3D Modelling Services in India etc.